Field Instrumentation
Installation & Calibration of Differential pressure transmitter (DPT)
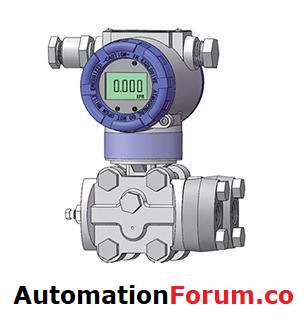
Table of Contents
Differential Pressure Transmitter
- The principle of differential pressure transmitter (DPT) level measurement is based on
hydrostatic head. - They are used in vessels that are open and enclosed. Usually, differential transmitters are connected to the side of a vessel or tank with insulation equipment.
Installation of DPT
- The capillary seal filled is susceptible to variations in ambient temperature. Protection should be considered, such as isolation shield, protective cover or installation facing the North.
- Diaphragm seals should have facility to maintain, remove, vent and drain (e.g. isolation features).
- The fitting of the flange should be mounted vertically. Installation of the diaphragm and capillary in vertical position
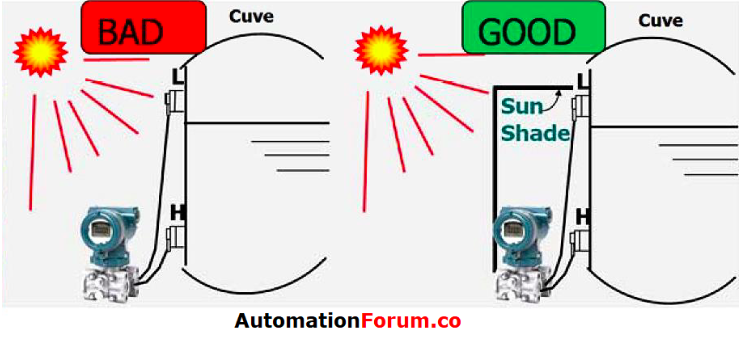
It is necessary to mount the differential pressure transmitter below the smallest point to be measured. The capillary position should prevent vaporization hazards.
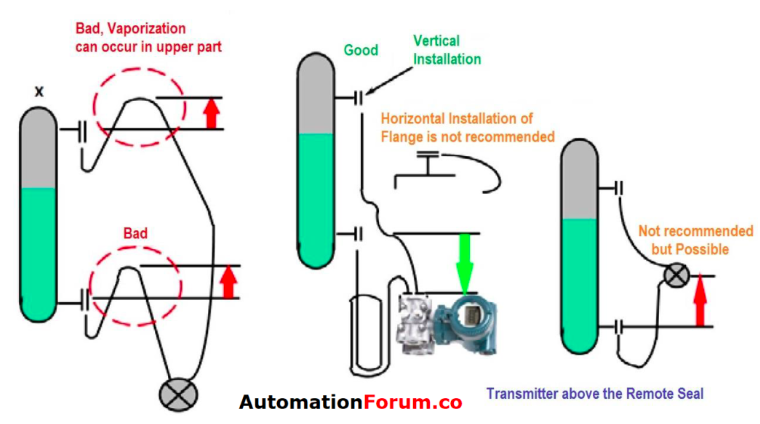
- Capillaries should have a minimum curvature radius of 150 mm, avoiding any vibration or friction.
- Diaphragm seals should be treated correctly in the field to prevent harm to the diaphragm seal and capillary tubing as well as possible loss of sensing fill fluid.
Calibration of DPT
At the Product Manufacturer premises, calibration should be conducted and checked prior to commissioning operations. A certificate of calibration should be given. A field pressure calibrator or a calibrator bench can be used to calibrate in site.
The oil column height should be taken into account to a zero offset
- When the tank is empty, the sensor measures the oil column’s LP weight, this value creates a zero offset in the negative that can be adjusted by zeroing with an empty ship during the period calibration or during conception.
- By calculation, the delta scale (or span) will usually be adapted in relation to the distance between the flanges and the liquid density, then added to the calculated zero value. Or with a complete ship it can be performed.
- Zero offset can be therefore even more important than the scale itself (especially with the fluorinated oil). We should choose a sensor whose extent of adjustment allows the zero offset.
- For measurements of density or multi-layer, it will be necessary to make the zero by adjusting 100% of the lightest liquid, the full scale will be calculated with 100% of the heaviest liquid.
LP side (upper connection), column vented to vessel atmosphere
- The sensor is null on both sides (HP and LP) when the tank is empty, then DP (differential pressure) is zero = 4 mA as well.
- When the tank is complete, measurement is height multiply by density, calibration is performed for 100 percent, calibration could be performed for another proportion if an intermediate level is known.
- Most significant thing: “This requires liquid not to enter the upper link, or the dry joint will be filled and this will create the zero offset.”
- Height should be continuous for density or multi-layer measurements, then it is obviously not feasible to use a dry leg, measurement should be performed in a ship that operates with overflow.