Interview Questions
Why not use 0-20mA & 0-15psi instead of 4-20mA & 3-15psi?
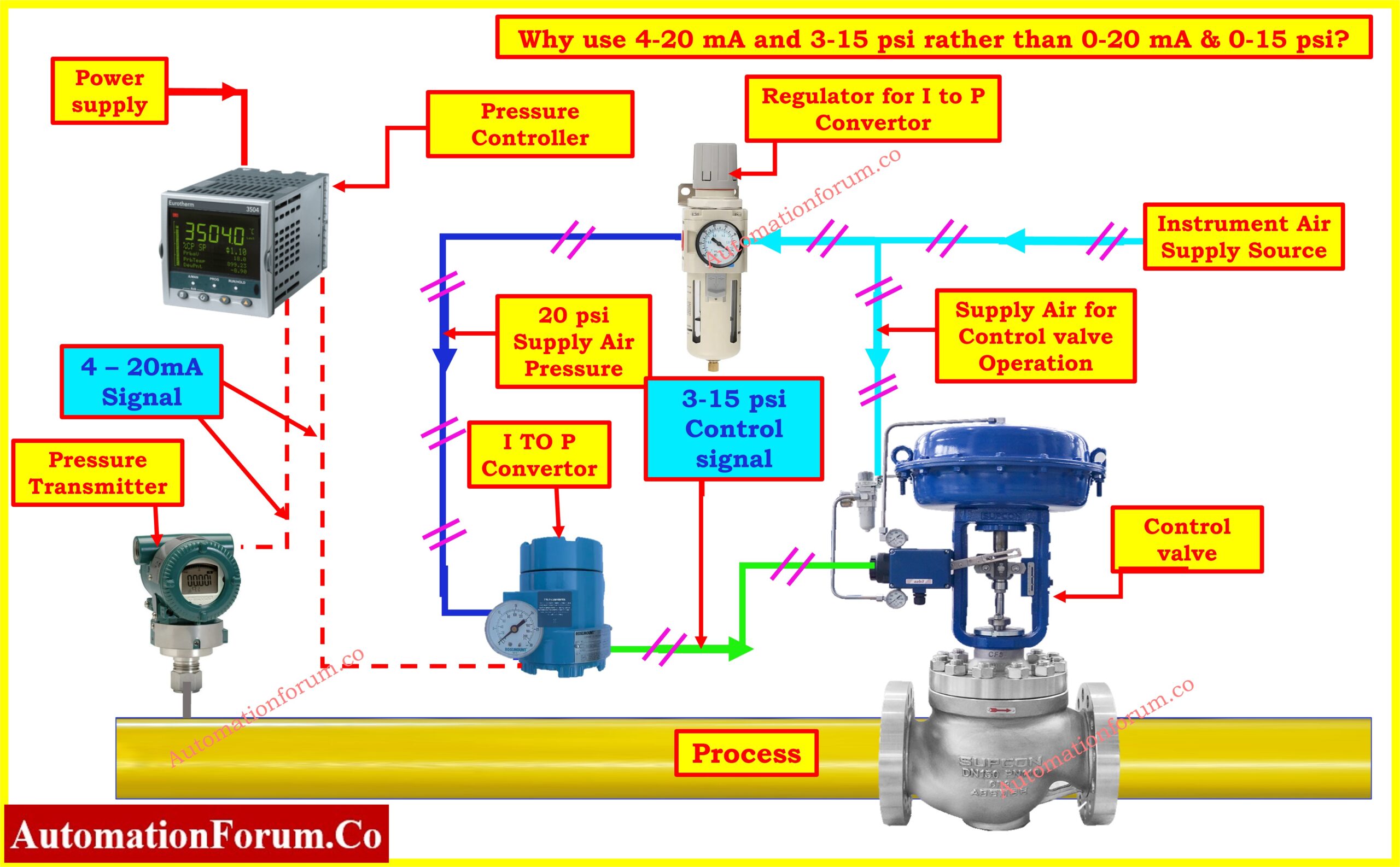
Table of Contents
- The implementation of standardized signal formats, such as the 4-20mA current loop and the 3-15 psi pressure signal, is common in industrial instrumentation and control systems.
- These formats support reliable and precise data transmission between sensors and control devices, thereby facilitating the monitoring and control of a variety of processes.
Understanding the 4-20mA Current Loop:
- Because of its simplicity and adaptability, the 4-20mA current loop is a two-wire communication technique that is frequently used in industrial settings.
- Information is conveyed through this system utilizing a current signal ranging from 4 to 20 milliamps.
- The current loop is made up of a receiver (or controller), a sensor (or transmitter), and a power supply. Temperature, pressure, or flow rate are examples of monitored parameters that are proportionately dependent on the current flowing through the loop.
Understanding the 3-15 psi Pressure Signal
- In pneumatic control systems, the 3-15 psi pressure signal is frequently utilized to convey data about parameters.
- The range of pressure in this format is 3 to 15 pounds per square inch (psi).
- This signal range is perfect for correctly reflecting different process conditions, much as the 4–20 mA current loop.
Why use 4-20 mA and 3-15 psi rather than 0-20 mA & 0-15 psi?
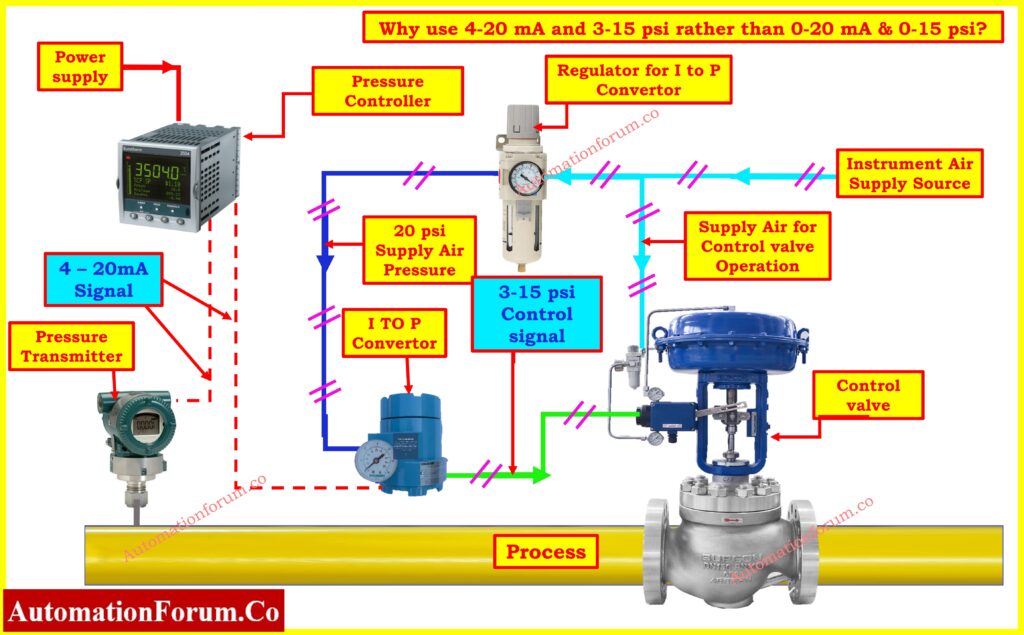
Advantages of 4-20 mA vs 0-20 mA
Fault Detection and Diagnostics:
- The 4-20 mA signal range allows for the distinction between a zero signal and a fault condition.
- At 4 mA, the signal represents the lowest measurement value or zero output. If the signal drops below 4 mA or exceeds 20 mA, it indicates a fault in the system, such as a broken wire or a malfunctioning sensor.
- This capability enables operators to quickly identify and address issues, minimizing downtime and ensuring operational efficiency.
Zero Offset Adjustment:
- Another advantage of the 4-20 mA signal is the ease of zero offset adjustment without the need for polarity change.
- By adjusting the zero offset, operators can calibrate the instrument to accurately measure the desired range of values within the 4-20 mA span.
- This flexibility simplifies calibration procedures and enhances the precision and reliability of measurements without requiring complex adjustments or modifications to the signal circuit.
Cost Efficiency with 2-Wire Systems:
- One of the primary advantages of using a 4-20 mA signal is the ability to operate with a 2-wire system.
- Unlike 0-20 mA signals which typically require 3 or 4 wires (two for power supply and one or two for signal transmission), the 4-20 mA configuration integrates both power supply and signal transmission into a single pair of wires.
- This reduction in wiring complexity leads to cost savings in terms of material, installation, and maintenance.
Integration of Power Supply and Signal Circuit:
- With 4-20 mA signals, the power supply and signal circuit are combined into one, simplifying the overall system design.
- This integration reduces the number of components required for signal transmission, minimizes points of failure, and streamlines troubleshooting and maintenance procedures.
Advantages of 3-15 psi vs 0-15 psi
Easier Pressure Regulation from 3 psi:
- One of the significant advantages of the 3-15 psi signal standard is that it starts from 3 psi rather than 0 psi.
- This starting point allows for easier pressure regulation and control, especially in pneumatic systems where precise adjustment of low-pressure settings is required.
- Starting from 3 psi provides a more stable baseline for controlling processes, minimizing the risk of pressure fluctuations and ensuring smoother operation.
No Need for Vacuum when Regulating to Zero Signal at 3 psi:
- In applications where a zero pressure signal is required, using the 3-15 psi standard eliminates the need to provide a vacuum to achieve this pressure level.
- With a minimum pressure setting of 3 psi, the system can maintain a positive pressure state even at the lowest signal level, simplifying system design and operation.
- This eliminates the complexity and cost associated with vacuum generation and ensures reliable performance, particularly in environments where vacuum systems may not be feasible or practical.
Distinguishing between Zero Pneumatic Signal and Pressure Failure:
- The 3-15 psi signal standard facilitates the distinction between a zero pneumatic signal and a pressure failure.
- Since the signal starts from 3 psi, any deviation from this baseline can be readily detected as a pressure anomaly or failure.
- This capability enhances system safety and reliability by providing operators with clear indications of pressure variations or malfunctions, allowing for timely intervention and maintenance to prevent potential hazards or disruptions to operations.
Click here for More Instrumentation Questions and Answers