Master Pressure Calibrators: Precision Tools for Accurate Pressure Instrument Calibration
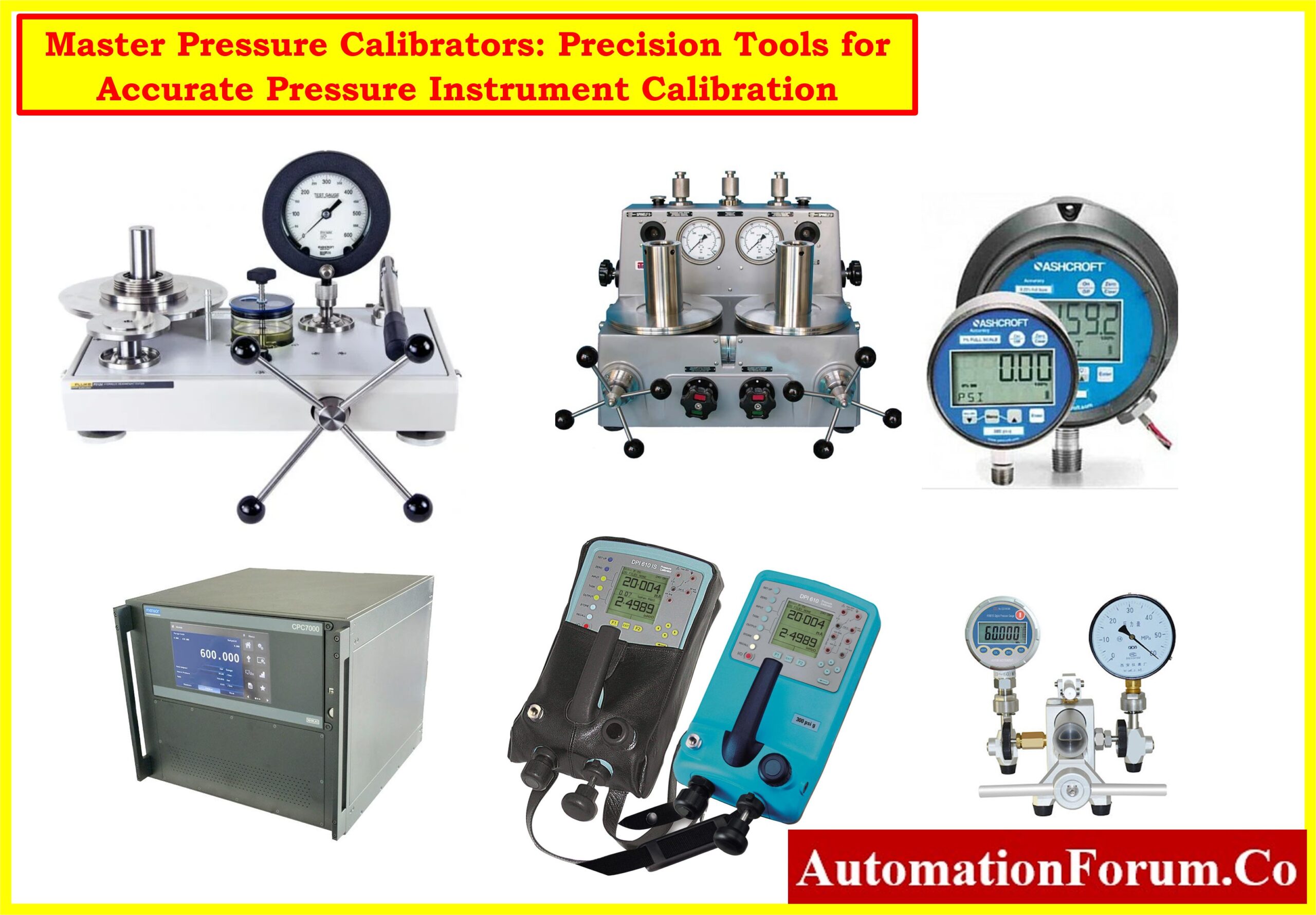
- Dead Weight Tester
- Top Manufacturers and Models of Dead Weight Tester
- Pressure Calibrators
- Top Manufacturers and Models of Pressure Calibrators
- Master Digital Pressure Gauges
- Features of Master Digital Pressure Gauges
- Top Manufacturers of Master Digital Pressure Gauges
- Manometers
- Top Manufacturers of Manometers for Calibration
- Hydraulic Pressure Standards
- Features of Hydraulic Pressure Standards
- Top Manufacturers of Hydraulic Pressure Standards
- Pneumatic Pressure Standards
- Features of Pneumatic Pressure Standards
- Top Manufacturers of Pneumatic Pressure Standards
- Pressure Comparators
- Features of Pressure Comparators
- Top Manufacturers of Pressure Comparators
- Comparison of Master Pressure Calibrators
- Pressure instrument calibration is a critical aspect of ensuring the accuracy and reliability of various industrial processes and measurements.
- To achieve precise calibrations, different types of master calibrators are employed, each tailored to specific pressure ranges and applications.
- This guide provides an in-depth exploration of the various master calibrators utilized in pressure instrument calibration, their principles of operation, advantages, limitations, and applications.
Dead Weight Tester
A Dead Weight Tester (DWT) is a device used to calibrate pressure measuring instruments. It operates on the principle of balancing the pressure applied to a piston-cylinder assembly against a set of known weights.
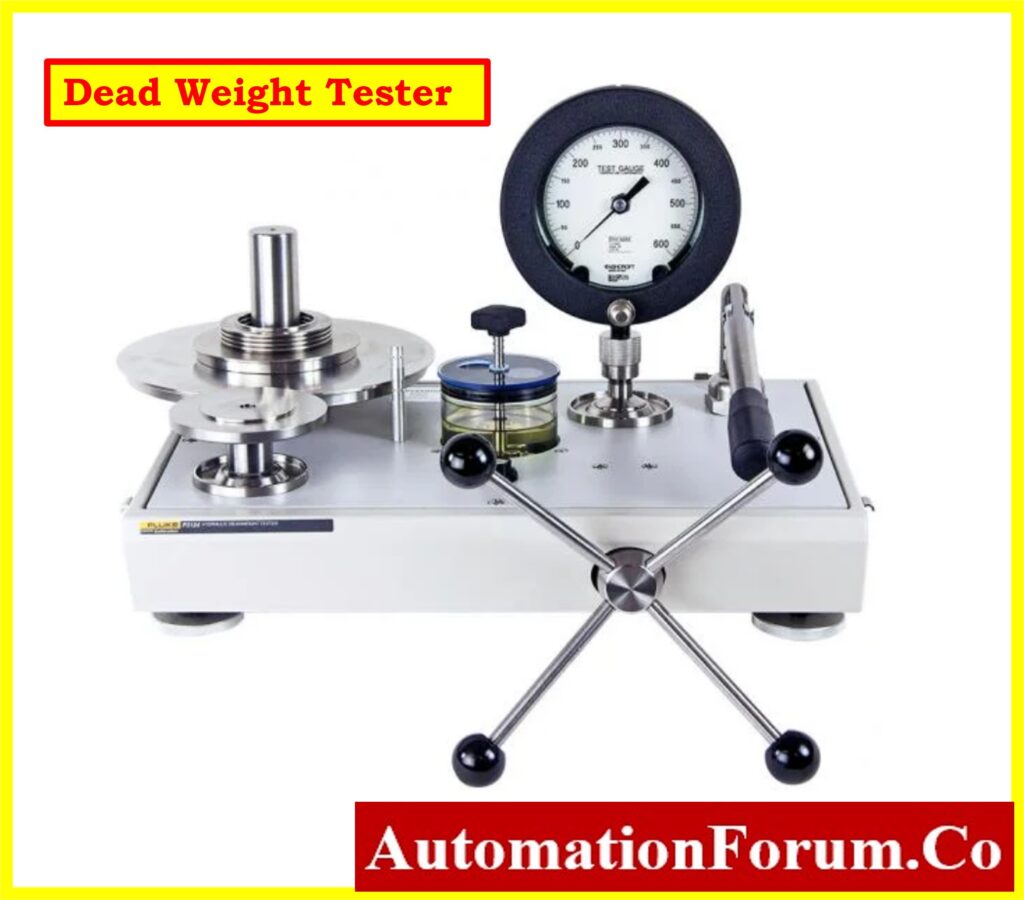
Here are some advantages, disadvantages, applications, and top manufacturers of Dead Weight Testers:
Advantages of Dead Weight Tester
- High accuracy: Dead Weight Testers offer very high levels of accuracy, often within 0.02% of the applied pressure.
- Wide pressure range: They can cover a wide range of pressures, from a few inches of water to thousands of PSI (pounds per square inch).
- Reliability: Once calibrated, Dead Weight Testers tend to maintain their accuracy over time, making them reliable tools for pressure calibration.
- Simple principle: The operation principle of DWT is straightforward, making it easy to understand and operate for skilled technicians.
Disadvantages of Dead Weight Tester
- Limited mobility: Dead Weight Testers are often heavy and bulky, limiting their portability and making them less suitable for field calibration.
- Setup time: Calibration using a Dead Weight Tester can be time-consuming, as it requires careful setup and adjustment.
- Sensitivity to environmental conditions: Changes in temperature, humidity, and altitude can affect the accuracy of Dead Weight Testers, necessitating careful environmental control during calibration.
Applications of of Dead Weight Tester
Dead Weight Testers are commonly used for calibrating various pressure measuring instruments, including:
- Pressure gauges
- Pressure transmitters
- Pressure switches
- Pressure sensors
- Pressure relief valves
Top Manufacturers and Models of Dead Weight Tester
Fluke Corporation:
Fluke offers a range of Dead Weight Testers under its “Fluke Calibration” brand, including
- P3100 Series Hydraulic Deadweight Testers
- P3200 Hydraulic Deadweight Tester
- P3830, P3840, and P3860 from the P3800 Series High Pressure Hydraulic Deadweight Testers
- E-DWT-HV Electronic Deadweight Tester
DH-Budenberg:
Refer below are the model numbers for DH-Budenberg’s dead weight testers:
Additionally, Budenberg offers a range of hydraulic dead weight testers with the following model numbers:
- BGH120
- BGH300
- BGH700
- BGH1200
- BGH1400
- BGH2600
- BGH4000
These models cover a variety of pressure ranges and are suitable for different calibration needs.
WIKA:
WIKA offers a variety of dead weight tester models, each designed for specific calibration needs. Here are some of the model numbers:
- CPB5800: This hydraulic dead weight tester is suitable for calibrations up to 1,400 bar (20,000 lb/in²)
- CPD8500: The digital dead weight tester offers a measuring range up to 500 bar (7,250 psi) and features an intuitive touchscreen user interface
- CPB3500: Available in different versions, including the compact CPB3800 and the high-pressure CPB3800HP, suitable for up to 2,600 bar (40,000 lb/in²)
These models are part of WIKA’s comprehensive range of dead weight testers, known for their precision and reliability in pressure calibration.
Additel:
Additel is known for its high-quality calibration equipment, including dead weight testers.
Mensor Corporation:
Mensor Corporation, which is part of the WIKA Group, offers a variety of dead weight tester models. Here are some of the model numbers you might be interested in:
- CPB6000: Primary Pressure Standard
- CPB5800: Pressure Standard
- CPB3800: Industrial Pressure Standard
- CPD8500: Digital Deadweight Tester.
These models are designed to serve as primary standards for pressure calibration in both laboratory and industrial applications.
Pressure Calibrators
Pressure calibrators are indispensable tools used to verify and adjust the accuracy of pressure measuring instruments across various industries.
Here’s a breakdown of their advantages, disadvantages, applications in calibration, and top manufacturers with their models:
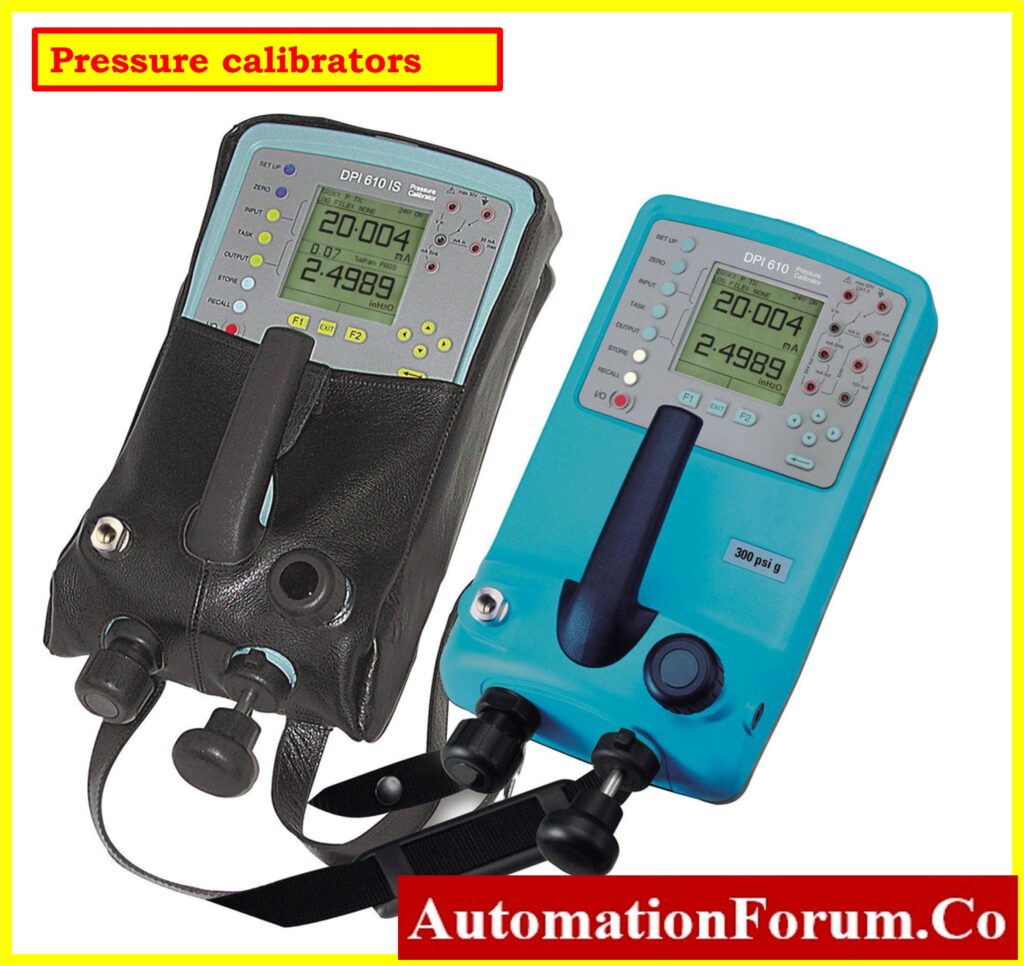
Advantages of Pressure Calibrators
- Pressure calibrators can be used to calibrate a wide range of pressure instruments, including gauges, transmitters, switches, sensors, and relief valves.
- High-quality pressure calibrators offer precise measurement capabilities, ensuring accurate calibration results.
- Portability: Many pressure calibrators are designed to be lightweight and portable, allowing for field calibration and on-site troubleshooting.
- Efficiency: Pressure calibrators streamline the calibration process, reducing downtime and improving productivity.Pressure calibrators can be used to calibrate a wide range of pressure instruments,
- They often feature multiple pressure ranges and measurement units, providing flexibility to accommodate different calibration requirements.
Disadvantages of Pressure Calibrators
- High-quality pressure calibrators can be expensive, especially models with advanced features and capabilities.
- Pressure calibrators themselves require periodic calibration to maintain accuracy, adding to the overall cost of ownership.
- Some pressure calibrators may have complex features and interfaces, requiring training for proper operation.
- Similar to dead weight testers, pressure calibrators can be sensitive to changes in temperature, humidity, and altitude, affecting calibration accuracy.
Applications of Pressure Calibrators in Calibration
- Oil and Gas Industry: Calibrating pressure gauges, transmitters, and sensors for drilling operations, pipeline monitoring, and refining processes. Ensuring safety and optimizing production efficiency in high-pressure environments.
- Petrochemical Industry: Verifying the accuracy of pressure instruments used in storage tanks, reactors, and pipelines. Preventing leaks, spills, and equipment failures through calibration.
- Pharmaceutical Industry:Calibrating pressure sensors and switches for precise pressure control in manufacturing processes. Ensuring product quality, regulatory compliance, and process consistency.
- Automotive Industry: Calibrating pressure sensors and gauges in automotive components like fuel systems and brake systems.
- HVAC (Heating, Ventilation, and Air Conditioning): Calibrating pressure instruments in HVAC systems, including air pressure sensors and differential pressure transmitters. Optimizing HVAC system performance, energy efficiency, and indoor air quality through calibration.
- Manufacturing Industry: Verifying the accuracy of pressure instruments in electronics, food and beverage production, and chemical processing. Ensuring quality assurance, process optimization, and equipment safety through accurate pressure control.
Top Manufacturers and Models of Pressure Calibrators
Druck:
- Druck DPI620 Genii: Multifunction calibrator combining pressure, electrical, and temperature calibrations.
- Druck DPI611: Robust pressure calibrator designed for field calibration. Features a touch screen interface for intuitive operation.
- Druck DPI 612 Flex Series: Modular calibrator system providing flexibility for pressure calibration tasks. Interchangeable pressure modules for various ranges and units.
- Druck DPI 705 Series: Compact and portable pressure calibrator ideal for on-site calibration. Simple interface and robust construction suitable for harsh environments.
Fluke Corporation:
- Fluke 718 Pressure Calibrator
- Fluke 729 Automatic Pressure Calibrator
- Fluke 750P Series Pressure Modules
WIKA:
- CPH7000 Portable Pressure Calibrator
- CPH6200 Precision Pressure Calibrator
- CPH6600 Hydraulic Pressure Calibrator
Additel:
- Additel 760 Digital Pressure Calibrator
- Additel 672 Manual Pressure Calibrator
- Additel 761-MA Automated Pressure Calibrator
Master Digital Pressure Gauges
Master digital pressure gauges are precision instruments designed specifically for calibration activities, offering high accuracy, reliability, and advanced features tailored for calibration purposes.
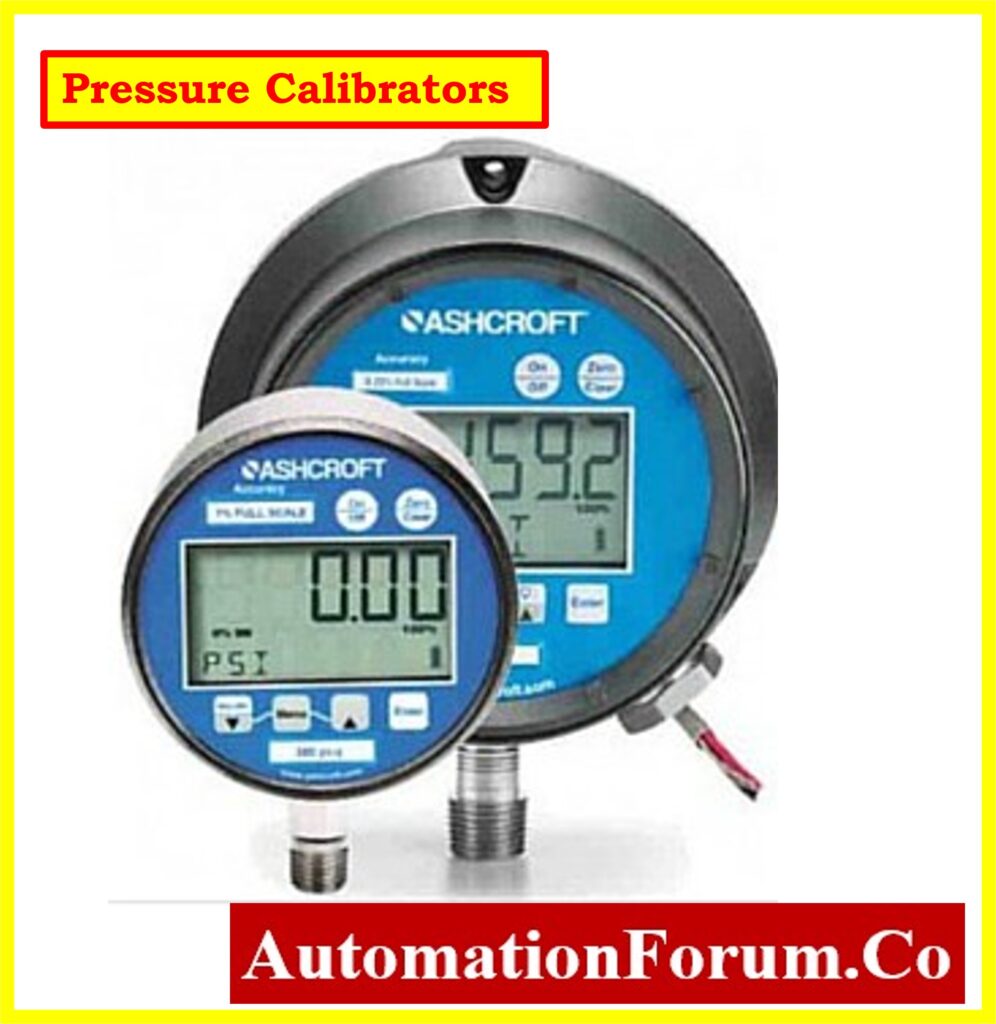
Here’s an overview of master digital pressure gauges for calibration activities:
Features of Master Digital Pressure Gauges
- High Accuracy: Master digital pressure gauges are characterized by their exceptional accuracy, often with calibration uncertainties as low as 0.01% of full scale.
- Reference Standard: They serve as reference standards for calibrating other pressure measuring instruments, ensuring traceability to international standards.
- Wide Measurement Range: Master digital pressure gauges typically cover a wide pressure range, allowing for calibration of instruments spanning low to high pressures.
- Multiple Units: They can measure and display pressure readings in various units, including psi, bar, kPa, MPa, and more, facilitating compatibility with different instruments.
- Calibration Capability: Many master digital pressure gauges have built-in calibration functions, allowing for on-site calibration verification and adjustment.
- Data Logging: Some models feature data logging capabilities, enabling the recording and storage of calibration results for documentation and analysis.
- Communication Interfaces: Master digital pressure gauges may include communication interfaces such as USB, RS-232, or Ethernet for data transfer and integration with calibration software.
Advantages of Master Digital Pressure Gauges for Calibration
- They provide highly accurate pressure references for calibrating a wide range of pressure instruments with confidence.
- Master digital pressure gauges streamline the calibration process, reducing calibration time and improving productivity.
- With their wide measurement range and multiple units, they can calibrate various pressure instruments across different industries and applications.
- Calibration using master digital pressure gauges ensures traceability to international standards, maintaining the integrity and reliability of calibration results.
- Built-in data logging capabilities enable efficient management and documentation of calibration records, supporting compliance with quality management systems.
Applications of Master Digital Pressure Gauges in Calibration
- Laboratory Calibration: They are used in calibration laboratories for verifying the accuracy of pressure measuring instruments such as pressure gauges, transmitters, and sensors.
- On-Site Calibration: Master digital pressure gauges can be deployed for on-site calibration activities in industries such as oil and gas, aerospace, automotive, and manufacturing.
- Quality Control: They play a crucial role in quality control processes by ensuring the accuracy and reliability of pressure instruments used in production and testing.
- Instrument Verification: Master digital pressure gauges are employed to verify the performance of pressure calibrators, dead weight testers, and other calibration equipment.
Top Manufacturers of Master Digital Pressure Gauges
Fluke Calibration:
- Fluke 700G Series: High accuracy, wide pressure range, rugged construction.
- Fluke 750 Series: Precision, versatility, advanced calibration features.
WIKA:
- WIKA CPG1500 Series: High accuracy, advanced features like data logging.
- WIKA CPG2500 Series: Exceptional accuracy, intrinsically safe options.
Additel Corporation:
- Additel 680 Series: Precision, user-friendly interfaces, advanced calibration functions.
- Additel 761 Series: Accuracy, versatility, data logging, communication interfaces.
GE Druck:
- GE Druck DPI 620 Genii Series: Combined calibration functions, high accuracy, ruggedness.
- GE Druck DPI 612 Flex Series: Modular design, interchangeable pressure modules, flexibility.
Mensor Corporation:
- Mensor CPC6000 Series: Primary pressure standards, exceptional accuracy and stability.
- Mensor CPC6050 Series: Advanced features, ease of use, communication interfaces.
Manometers
Manometers are essential tools in calibration activities for measuring and calibrating pressure instruments. They come in various types, including mercury manometers, liquid-column manometers, and digital manometers. Here’s an overview of manometers used in calibration activities:
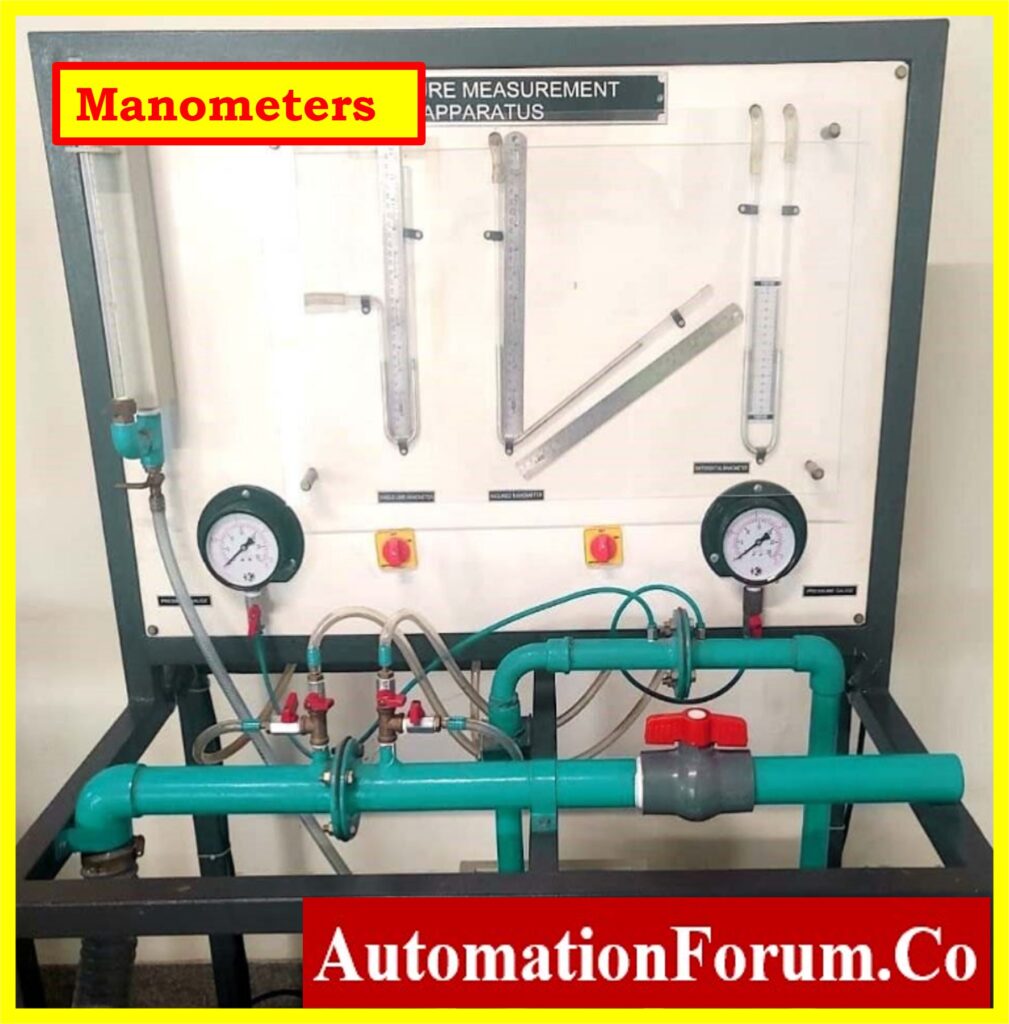
Mercury Manometers:
- Traditional but highly accurate instruments.
- Use a vertical glass tube filled with mercury.
- Offer exceptional accuracy and reliability.
- Suitable for laboratory calibration due to high precision.
- Safety and environmental concerns due to mercury’s toxicity and proper disposal requirements.
Liquid-Column Manometers:
- Utilize a liquid column (not mercury) to measure pressure.
- Offer good accuracy and reliability for calibration purposes.
- Can be filled with water, oil, or other suitable fluids.
- Provide direct measurement of pressure based on fluid displacement.
- Safer alternative to mercury manometers but still require proper handling and disposal.
Digital Manometers:
- Modern electronic instruments for pressure measurement.
- Offer high accuracy and versatility.
- Feature digital displays for easy reading and interpretation.
- Often portable and suitable for field calibration activities.
- Provide additional features such as data logging, communication interfaces, and pressure unit conversion.
Applications of Manometer in Calibration
- Manometers are used to calibrate pressure gauges, transmitters, sensors, and switches.
- They serve as reference standards for verifying the accuracy of pressure measuring instruments.
- Manometers are employed in laboratory calibration as well as on-site calibration activities.
- They play a crucial role in ensuring the accuracy and reliability of pressure measurements across various industries and applications.
Top Manufacturers of Manometers for Calibration
- WIKA: WIKA offers a wide range of manometers known for their accuracy and reliability, suitable for laboratory and industrial calibration.
- Ashcroft: Ashcroft produces high-quality manometers with advanced features for calibration and measurement applications.
- Fluke: Fluke manufactures digital manometers renowned for their precision and versatility in calibration activities.
- GE Druck: GE Druck provides reliable manometers designed for precision calibration activities, offering high performance and durability.
Disadvantages of using Manometers
- Mercury Manometers pose significant concerns due to their toxicity and environmental impact. Handling and disposal require meticulous care to mitigate health risks and prevent environmental contamination.
- Liquid-Column Manometers, while effective, have limitations. Their pressure range may not adequately cover high-pressure calibration needs. Additionally, the choice of fluid can impact accuracy and performance, necessitating careful consideration in calibration activities.
Hydraulic Pressure Standards
Hydraulic pressure standards are essential tools in calibration activities, providing accurate and reliable references for calibrating pressure instruments. Here’s an overview of hydraulic pressure standards and their role in calibration:
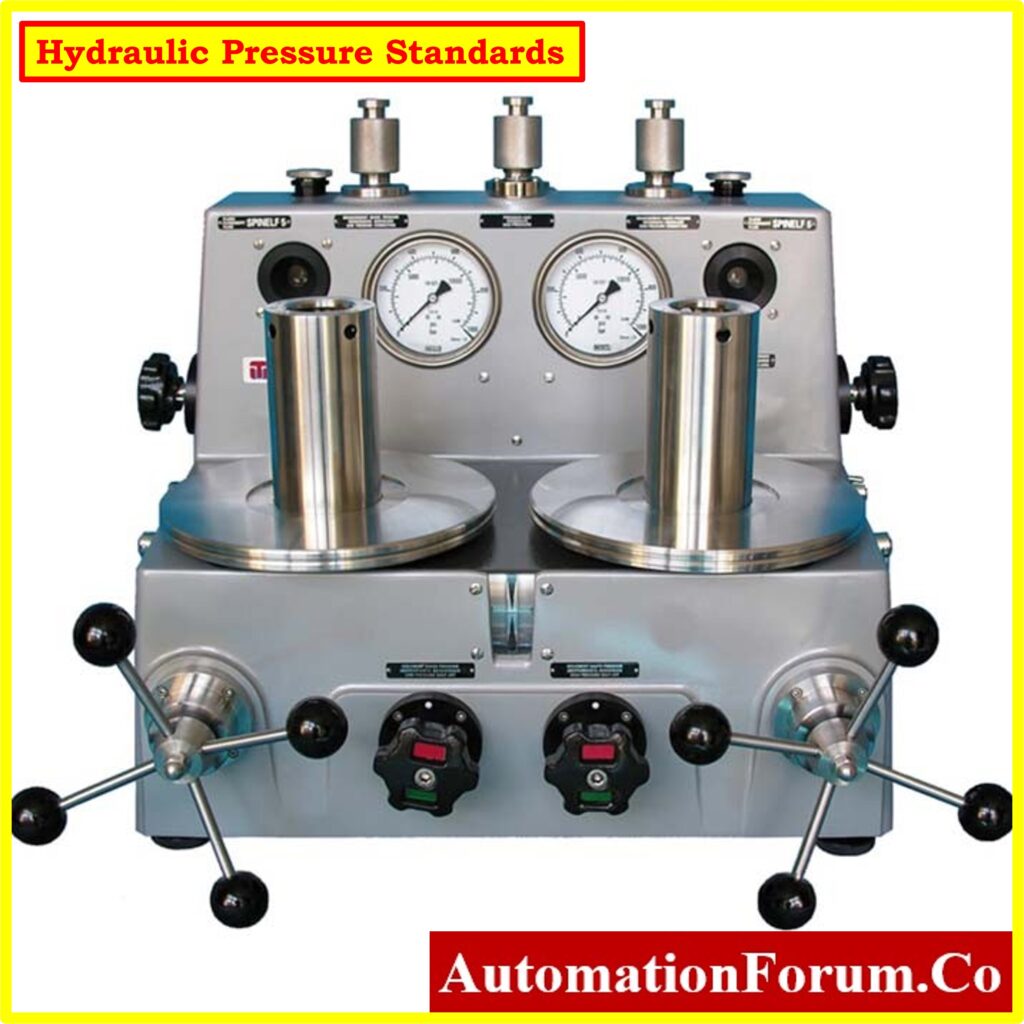
Features of Hydraulic Pressure Standards
- Hydraulic pressure standards utilize fluid mechanics principles to generate and control pressure accurately.
- They offer exceptional accuracy, often with uncertainties as low as 0.01% of full scale.
- Hydraulic standards cover a broad pressure range, from low to high pressures, catering to various calibration needs.
- Hydraulic systems are known for their stability over time, ensuring consistent and reliable pressure references.
- Many hydraulic standards allow for precise adjustment and control of pressure levels, facilitating calibration tasks.
Advantages of Hydraulic Pressure Standards
- Hydraulic pressure standards provide precise and reliable pressure references for calibrating pressure instruments with confidence.
- They cover a wide pressure range, making them versatile for calibrating instruments across different industries and applications.
- Hydraulic systems offer stability and repeatability, ensuring consistent calibration results over time.
- Many hydraulic standards feature adjustable pressure levels, allowing for calibration at specific pressure points as needed.
Applications of Hydraulic Pressure Standards in Calibration
- Hydraulic pressure standards are used in calibration laboratories for verifying the accuracy of pressure measuring instruments such as pressure gauges, transmitters, and sensors.
- They serve as primary pressure standards for maintaining traceability to international standards in calibration activities.
- Hydraulic standards are employed in on-site calibration activities in industries such as aerospace, automotive, oil and gas, and manufacturing.
Top Manufacturers of Hydraulic Pressure Standards
Here are the model numbers for hydraulic pressure standards from the top manufacturers you’ve mentioned:
- Fluke Calibration:
- WIKA: CPB6000 Primary Standard Pressure Balance
- Additel Corporation: ADT762W Automated Hydraulic Pressure Calibrator
- Mensor Corporation: CPC8000-H Precision Hydraulic High-Pressure Controller
Pneumatic Pressure Standards
Pneumatic pressure standards are instruments used in calibration to generate and control pneumatic pressure for calibrating pressure measuring devices. Here’s an overview of pneumatic pressure standards and their role in calibration activities:
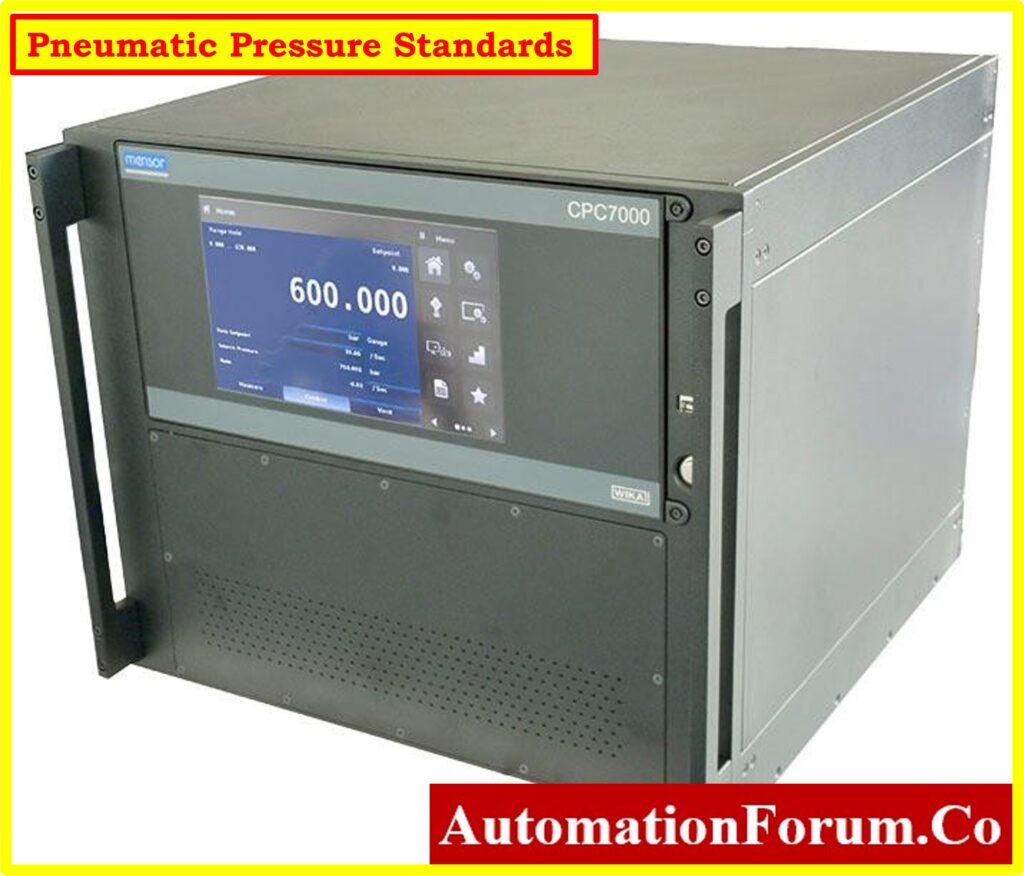
Features of Pneumatic Pressure Standards
- Pneumatic System: Pneumatic pressure standards use compressed air or gas to generate and control pressure.
- Pressure Control Mechanism: They typically incorporate valves, regulators, and precision components to control and stabilize the generated pressure.
- High Accuracy: Pneumatic pressure standards offer high accuracy and repeatability in pressure generation and control.
- Adjustability: Many pneumatic standards allow for precise adjustment of pressure levels to match specific calibration requirements.
- Pressure Measurement: They often include built-in pressure measurement devices such as digital manometers or transducers to monitor the generated pressure.
- Portability: Some pneumatic pressure standards are designed to be portable, allowing for on-site calibration activities.
Applications of Pneumatic Pressure Standards in Calibration
- Pneumatic pressure standards are used in calibration laboratories for verifying the accuracy of pressure measuring instruments.
- They serve as primary pressure standards for maintaining traceability to international standards in calibration activities.
- Pneumatic pressure standards are employed in on-site calibration activities in industries such as aerospace, automotive, oil and gas, and manufacturing.
Top Manufacturers of Pneumatic Pressure Standards
The top manufacturers of pneumatic pressure standards are known for their precision and reliability in the calibration industry. Here are some of the model numbers for their pneumatic pressure standards:
- Fluke Calibration: P3000 Series Pneumatic Deadweight Testers
- Additel Corporation:
- Mensor Corporation:
Pressure Comparators
Pressure comparators are devices used in calibration to compare the pressure generated by a reference standard against the pressure measured by the device under test (DUT). Here’s an overview of pressure comparators and their role in calibration activities:
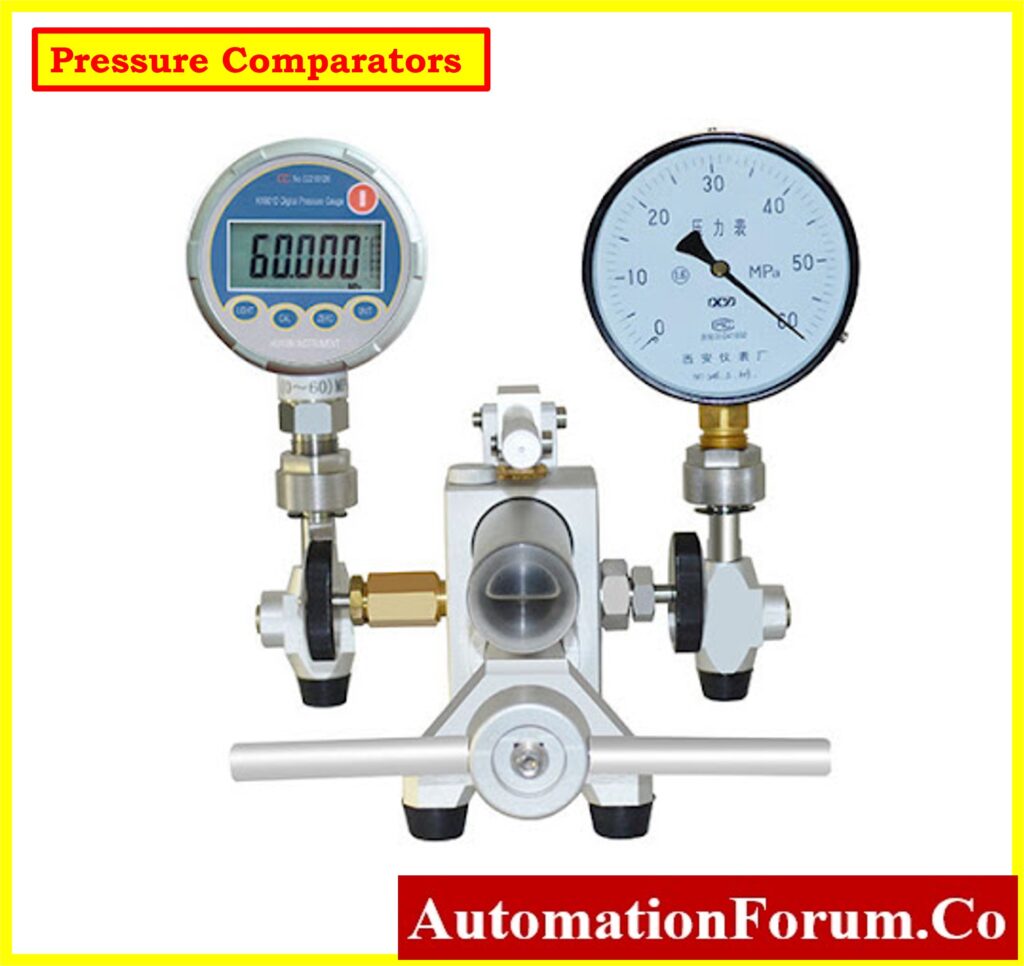
Features of Pressure Comparators
- Piston-Cylinder Assembly: Pressure comparators typically consist of a piston-cylinder assembly where pressure is generated and controlled.
- Hydraulic or Pneumatic Operation: They may operate using either hydraulic fluid or compressed air to generate pressure, depending on the design.
- Precise Pressure Control: Pressure comparators provide precise control over the generated pressure, allowing for accurate comparison with the DUT.
- High Accuracy: They offer high accuracy in pressure measurement, ensuring reliable calibration results.
- Adjustability: Many pressure comparators feature adjustable pressure levels, allowing for calibration at specific pressure points.
- Ease of Use: They are designed to be user-friendly, with intuitive controls and interfaces for calibration technicians.
Advantages of Pressure Comparators
- Pressure comparators provide precise pressure references for calibrating pressure instruments with confidence.
- They can be used to calibrate a wide range of pressure instruments, including pressure gauges, transmitters, sensors, and switches.
- Pressure comparators offer stability and repeatability in pressure generation, ensuring consistent calibration results over time.
- Many pressure comparators can accommodate various pressure ranges and units, making them suitable for diverse calibration needs.
Applications of Pressure Comparators in Calibration
- Pressure comparators are used in calibration laboratories for verifying the accuracy of pressure measuring instruments.
- They serve as primary pressure standards for maintaining traceability to international standards in calibration activities.
- Pressure comparators are employed in on-site calibration activities in industries such as aerospace, automotive, oil and gas, and manufacturing.
Top Manufacturers of Pressure Comparators
The top manufacturers of pressure comparators and some of their model numbers are:
- Additel Corporation: Known for a variety of pressure calibration equipment, including the Additel 761A Series Automated Pressure Calibrators.
- Ametek STC: Offers the P Series Pressure Comparator (System D) and Type T Pressure Comparator (System F).
- AREMECA: While specific model numbers were not retrieved, they are listed as a notable manufacturer.
- ASHCROFT: Provides the 1327D Pressure Gauge Comparator.
- Fluke Calibration: Offers models like the P5514B Hydraulic Pressure Comparator.
- Indumart: Features the PCM800 Series with models like PCM810 and PCM820.
Comparison of Master Pressure Calibrators
The comparison outlines diverse pressure calibration devices, from Dead Weight Testers to Master Digital Pressure Gauges, emphasizing principles, accuracy, range, mobility, setup, and applications.
Feature | Dead Weight Tester | Pressure Calibrator | Master Digital Pressure Gauge | Manometer | Hydraulic Pressure Standard | Pneumatic Pressure Standard | Pressure Comparator |
Principle of Operation | Balancing pressure against known weights | Direct pressure application | Digital measurement of applied pressure | Fluid displacement in a column | Fluid mechanics for pressure generation | Compressed air/gas pressure generation | Comparison of pressure between reference standard and device under test |
Accuracy | Very high (typically 0.02% of applied pressure) | High | Exceptional (typically 0.01% of full scale) | High | Exceptional (typically 0.01% of full scale) | High | High |
Pressure Range | Wide (from inches of water to thousands of PSI) | Wide | Wide | Varies based on type | Broad (from low to high pressures) | Broad | Varies based on model |
Mobility | Limited (heavy and bulky) | Portable | Portable | Varies based on type | Varies based on type | Portable | Portable |
Setup Time | Time-consuming | Variable | Variable | Variable | Variable | Variable | Variable |
Environmental Sensitivity | Sensitive | Sensitive | Sensitive | Sensitive | Stable over time | Stable over time | Stable over time |
Applications | Pressure gauges, transmitters, switches, sensors, relief valves | Pressure instruments across industries | Calibration activities | Pressure instruments | Calibration laboratories, on-site calibration | Calibration activities | Calibration activities |